Rapid prototyping of drone components using 3D printing
- Mahendra Lokhande
- Feb 1
- 1 min read
Updated: Feb 11
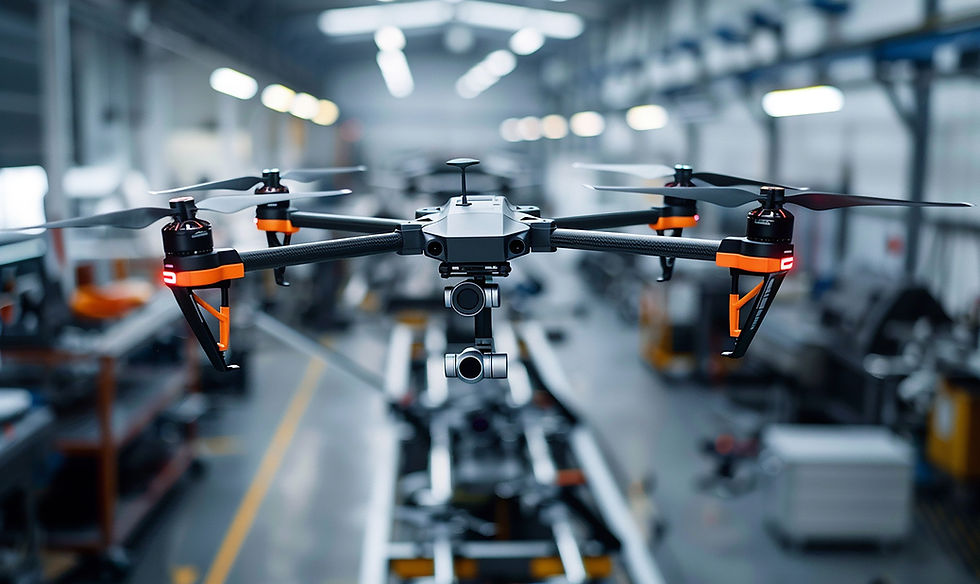
Challenge:
A startup, specializing in drone technology, aimed to create a new drone model that required several custom components, including airframes, landing gear, and motor mounts. The traditional manufacturing methods posed significant challenges, including high costs, long lead times, and inflexibility in design changes. The startup needed a rapid prototyping solution that would allow them to iterate designs quickly and efficiently while maintaining high quality.
Solution:
Collaborated with the client’s engineering team to ensure that all designs were optimized for performance and manufacturability.
Chose suitable materials such as PLA and ABS for their balance of durability and weight, ensuring that the components could withstand the operational stresses of drone flight.
Considered advanced materials like nylon for specific parts that required enhanced strength and flexibility.
Employed Fused Deposition Modeling (FDM) technology for its efficiency in producing complex geometries quickly.
Outcome:
The collaboration yielded several significant results:
Accelerated Development Cycle: The startup was able to reduce the prototyping phase from several months to just a few weeks. This rapid turnaround allowed them to bring their new drone model to market significantly faster.
Cost Efficiency: By utilizing 3D printing, the startup achieved a 40% reduction in prototyping costs compared to traditional manufacturing methods. This allowed them to allocate resources toward further innovation and development.
Comments